One common issue among reloaders is the difficulty in seating bullets, which can lead to dented or marked projectiles, as well as damaged seating stems. These problems often arise from the high forces required to seat a bullet properly. To address this, we conducted a series of tests using an AMP Press to better understand how various factors, such as sizing techniques, lubricants, neck tension, and brass and bullet manufacturers, impact seating pressures.
In this test, we used a 6.5×47 full-length sizing die, paired with two different expander balls—.262″ and .2635″—to create different levels of neck tension. The .262″ expander produced roughly .003″ to .0035″ of neck tension, while the .2635″ expander resulted in .0015″ of neck tension. Using neck tension gauges and calipers, we were able to measure the exact tension by comparing the sized brass to the loaded rounds (e.g., a sized brass neck measuring .287″ would measure .289″ when the bullet is seated, indicating .002″ of neck tension).
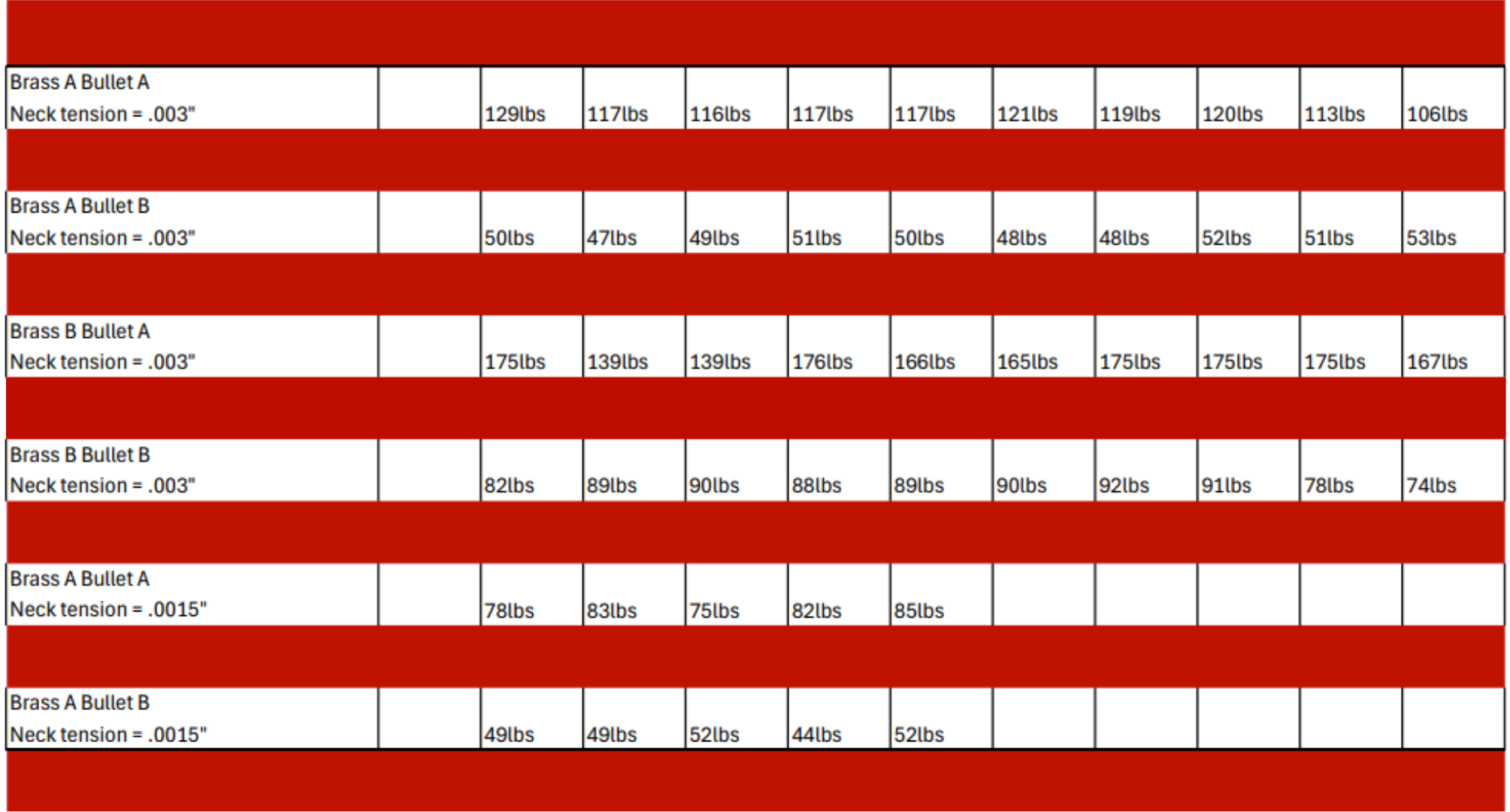
The test included brass from two different manufacturers (Brass A and Brass B) and two different bullets (Bullet A and Bullet B). While the results are not perfect, they clearly illustrate some important findings about seating forces:
- Bullet Type Matters: The type of bullet used can have a significant impact on seating force. With Bullet B, the seating force remained nearly identical, regardless of the neck tension (.003″ vs. .0015″), suggesting that for this bullet, neck tension doesn’t significantly affect the seating pressure. This is consistent with other tests that show neck tension between .001″ and .004″ has little impact on seating force.
- Anomaly with Bullet A: The most interesting finding came with Bullet A. The seating force was noticeably lower when using a .003″ neck tension compared to .0015″, with the difference being about half. This was unexpected, as prior tests had not shown such a significant change with neck tension. While it remains an outlier, it highlights the complexity of how different bullet designs interact with neck tension.
This testing is an important step in understanding the nuances of reloading. Forster’s goal is not only to refine reloading practices but also to understand what causes some of these common frustrations, such as excessive seating forces. Our plans going forward are to continue these tests to provide more insight for reloaders, both novice and experienced, to improve their processes and avoid common pitfalls.
For a deeper look at the testing process and to see the experiment in action, be sure to check out the video below—it’s a great way to visualize the findings and gain further insights into how these variables affect seating forces.
Stay tuned for more updates as Forster Products explores these variables in further detail to help the reloading community.