Selecting the correct bushing size for your resizing die is crucial for achieving the right neck tension. If the bushing is too large, the brass won’t securely hold the bullet. Too small, and the brass can become overworked. We want to share some practical methods we use to help you find the perfect bushing size for your needs.
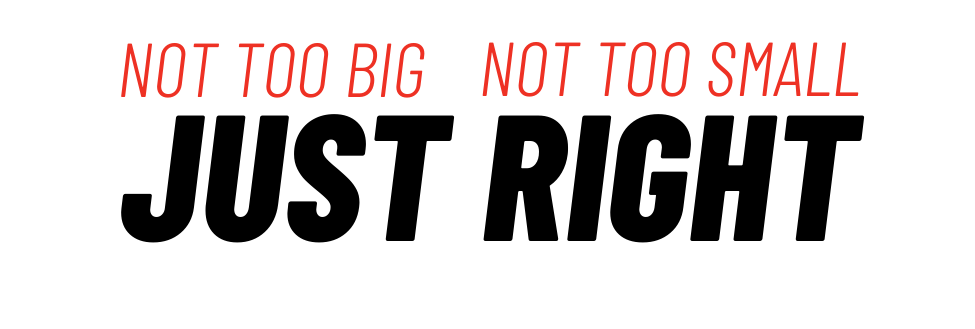
Two Methods for Finding the Right Busing Size:
1. Wall Thickness Method:
- Measure the neck wall thickness and multiply it by 2.
- Add the bullet diameter, then subtract 0.002”.
- Example for a 6.5mm: Wall thickness = 0.014” x 2 = 0.028” + 0.264” = 0.292” – 0.002” = 0.290” bushing.
- Note: This method can be tricky with basic tools like calipers. For more accuracy, a ball micrometer is ideal.
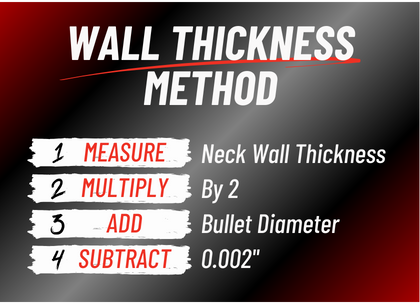
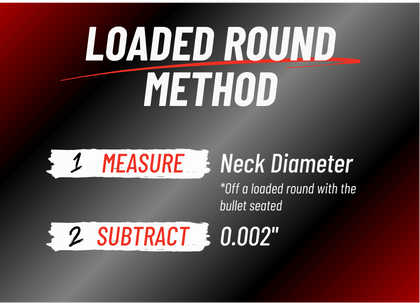
2. Loaded Round Method:
- Measure the neck diameter of a loaded round with the bullet seated.
- Subtract 0.002” from that measurement.
- Example: Loaded round neck diameter = 0.292” – 0.002” = 0.290” bushing.
Keep in mind that these methods are approximate. Variables like brass hardness, spring-back, and bushing variations can impact the results.
Adjusting for Your Needs:
The above methods aim to get you close to the industry-standard 0.002” neck tension, which ensures that bullets won’t shift during cycling or handling. However, different shooting styles may require adjustments:
- Hunters and field match shooters may prefer tighter neck tension (0.003” – 0.004”), which would need a smaller bushing and possibly a custom-polished expander ball.
- Benchrest shooters may go for as little as 0.0005” – 0.001” tension for ultimate precision.
A Tip for Precision: When using a bushing die, some shooters skip the expander ball altogether or use a mandrel. While this can be effective, it may lead to inconsistencies if the brass isn’t perfectly concentric. I prefer using a slightly smaller bushing paired with an expander ball, which allows me to pull the brass through and correct any alignment issues from the inside out.
For example, with my 6.5x47L brass, my loaded round measures 0.2895”. I use a 0.286” bushing and a 0.262” expander ball to achieve a consistent 0.0025” – 0.003” neck tension. This ensures that my neck is being properly sized and any imperfections are corrected during the process.
Remember: A properly sized expander ball is just as important as the right bushing. If you’re not using an expander ball or mandrel, you can ignore this step—but it’s crucial if you do.
Why Not Use a Standard Die?
Standard sizing dies can overwork the brass, especially if it’s thicker. This is where a bushing die can be beneficial, allowing you to maintain consistency without overworking your brass.
If you have any questions or need help choosing the right bushing, feel free to reach out. We’re here to help you achieve the precision you’re aiming for.
Happy shooting,
Forster Products